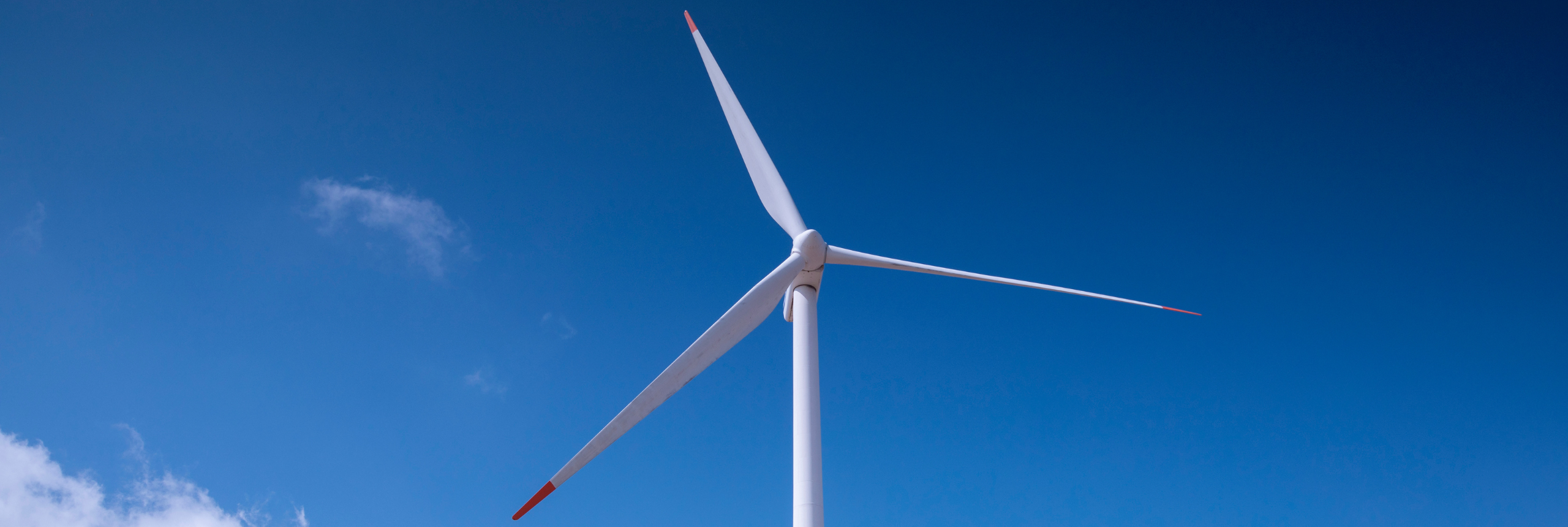
Blogs
How Better Data Can Protect Wind Farms from Icing Risks
Icing on wind turbine blades isn’t just a seasonal nuisance—it’s a significant financial and operational risk for wind farms. Ice accumulation can cause turbine shutdowns, lost energy production, increased wear on components, and dangerous safety hazards. Despite these risks, many wind farms rely on outdated feasibility studies and inaccurate models to estimate icing-related losses.
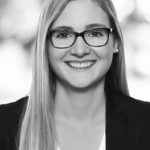
Daniela Roeper, P.Eng.
Vice President BorealisWind
Traditional assessments often fail to capture the true impact of icing due to incomplete meteorological data, reliance on historical averages, and inaccurate perceptions of climate change. This results in underestimated energy losses, unplanned downtime, and costly repairs that could have been avoided with a more data-driven approach. Understanding your icing class, leveraging comprehensive ice detection systems, and analyzing climate trends are key steps toward accurately assessing and mitigating icing risks.
Understanding Icing Classes
Studies show that icing can reduce AEP by 3-20%, depending on the severity of conditions (NREL Study).
One of the most critical factors in assessing icing risk is understanding icing classes, which categorize the severity and frequency of ice accumulation at a given wind farm location. These classifications help operators estimate potential energy losses and the likelihood of extended turbine downtime.
Figure 1. IEA Ice classification table (WIceAtlas | Methodology)
Without knowing your farm’s icing class, you could be severely underestimating your energy losses. For example, a wind farm in Icing Class 2 might lose 8% of annual energy production (AEP), whereas a wind farm in Icing Class 4 could see 15-20% losses if left unprotected. These losses translate directly into millions of Euros in unrealized revenue. It’s also important to remember that production loss due to icing can impact revenue even more significantly in open markets. When production drops, prices tend to rise, meaning the financial impact of icing can be significantly amplified.
The Problem with Feasibility Studies
Feasibility studies are a crucial part of wind farm development and financial modeling, but they often underestimate icing losses due to poor data collection methods. Many studies rely on generic climate models for broad regions that don’t always capture site specific conditions. Relying on historical averages to predict weather patterns can be problematic because patterns have changed over the last decade.
Underestimating icing losses in feasibility studies means that financial models are inaccurate, leading to unexpected revenue shortfalls, higher maintenance costs, and lower-than-expected ROI.
Climate Change and Increasing Icing Severity
A common misconception is that global warming will reduce icing risks. However, recent data has shown the opposite—icing events are becoming not only more severe but also more frequent. In the data measured from our ice protection systems, we’ve observed a slight increase in icing severity over time.
Rising global temperatures lead to more moisture in the air, which increases the likelihood of freezing rain and ice buildup on turbine blades. More extreme weather patterns mean icing events are lasting longer and occurring more often. The warmest years on record have still seen progressively severe icing conditions due to shifts in atmospheric moisture levels (NOAA Climate Report).
As these patterns continue to evolve, wind farms should expect icing to be a more persistent issue, making proactive solutions even more critical for long-term performance.
The Importance of Ice Detection and Monitoring
Wind farm operators often don’t realize how much energy they’re losing due to icing because they lack proper ice detection systems. Real-time monitoring provides critical data that helps operators take action before ice-related shutdowns occur. Missing or ignoring ice detection data leads to more downtime, increased safety risks, and unnecessary financial losses.
Ice detection systems can improve operations by providing accurate measurement of icing duration and severity using real-time sensors that detect icing conditions and trigger automatic alerts or ice mitigation systems. Additionally, scheduled maintenance based on actual data can prevent costly, unplanned repairs.
Make Data Work for Your Wind Farm
Ignoring the risks related to icing or outdated methods of measuring the impact of icing on your turbines can lead to significant financial, operational, and reputational losses. As technology advances faster every day, there is more data available than ever to improve your approach to maximizing turbine efficiency and safety.
Take the right steps forward to make data work for your wind farm:
- Evaluate your current icing risk assessment methods – Are you using accurate, site-specific data?
- Invest in real-time monitoring and ice detection and identify problems before they impact production.
- Consider ice protection systems – comprehensive solutions can recover more than 70% of lost energy due to icing.
Your wind farm’s profitability may depend on how well you understand and mitigate icing risks. Don’t wait until you start losing money – make data driven decisions to protect your turbines and your wallet.
Additional Information
How the BorealisWind Ice Protection System works
Sources
An Overview of Wind-Energy-Production Prediction Bias, Losses, and Uncertainties
Best-Practices-for-Wind-Farm-Icing-and-Cold-Climate_June2020.pdf